French Solar Energy Institute Ines har udviklet nye PV -moduler med termoplast og naturlige fibre, der er hentet i Europa, såsom hør og basalt. Forskerne sigter mod at reducere det miljømæssige fodaftryk og vægt af solcellepaneler, mens de forbedrer genbrug.
Et genanvendt glaspanel på fronten og en linnedkomposit på bagsiden
Billede: Gd
Fra PV -magasinet Frankrig
Forskere ved Frankrigs National Solar Energy Institute (INES)-en afdeling af de franske alternative energier og Atomic Energy Commission (CEA)-udvikler solmoduler med nye biobaserede materialer i forsiden og bagsiden.
”Da kulstofaftrykket og livscyklusanalysen nu er blevet væsentlige kriterier i valget af fotovoltaiske paneler, vil sourcing af materialer blive et afgørende element i Europa i de næste par år,” sagde Anis Fouini, direktøren for CEA-ines , i et interview med PV -magasinet Frankrig.
Aude Derrier, forskningsprojektets koordinator, sagde, at hendes kolleger har set på de forskellige materialer, der allerede findes, for at finde et, der kunne give modulproducenter mulighed for at producere paneler, der forbedrer ydeevne, holdbarhed og omkostninger, mens de sænker miljøpåvirkningen. Den første demonstrator består af heterojunction (HTJ) solceller integreret i et alt-sammensat materiale.
”Forsiden er lavet af en fiberglasfyldt polymer, der giver gennemsigtighed,” sagde Derrier. "Bagsiden er lavet af sammensat baseret på termoplast, hvor en vævning af to fibre, hør og basalt, er blevet integreret, hvilket vil give mekanisk styrke, men også bedre modstand mod fugtighed."
Høren er hentet fra det nordlige Frankrig, hvor hele det industrielle økosystem allerede er til stede. Basalt er hentet andetsteds i Europa og er vævet af en industriel partner af INES. Dette reducerede kulstoffodaftrykket med 75 gram CO2 pr. Watt sammenlignet med et referencemodul med samme effekt. Vægten blev også optimeret og er mindre end 5 kg pr. Kvadratmeter.
”Dette modul er rettet mod PV -taget og bygningsintegration,” sagde Derrier. ”Fordelen er, at det naturligt er sort i farve uden behov for et bagark. Med hensyn til genanvendelse, takket være termoplast, der kan remeltes, er adskillelsen af lagene også teknisk enklere. ”
Modulet kan fremstilles uden at tilpasse de nuværende processer. Derrier sagde, at ideen er at overføre teknologien til producenterne uden yderligere investeringer.
”Det eneste imperativ er at have frysere til at opbevare materialet og ikke at starte harpikets tværbindingsproces, men de fleste producenter i dag bruger Prepreg og er allerede udstyret til dette,” sagde hun.
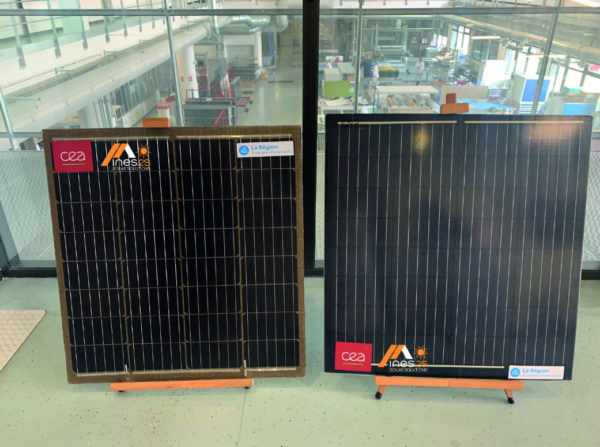
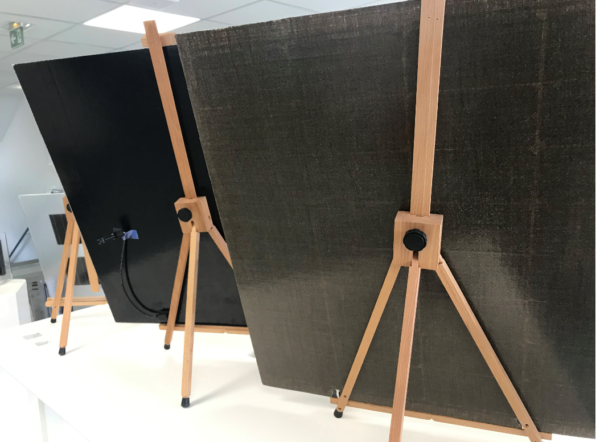
”Vi arbejdede på glasets anden liv og udviklede et modul bestående af genbrugt 2,8 mm glas, der kommer fra et gammelt modul,” sagde Derrier. ”Vi har også brugt et termoplastisk indkapslingsmiddel, som ikke kræver tværbinding, som derfor vil være let at genbruge, og en termoplastisk sammensætning med hørfiber til modstand.”
Den basaltfri bagfra af modulet har en naturlig linnedfarve, som for eksempel kan være æstetisk interessant for arkitekter med hensyn til facadeintegration. Derudover viste INES -beregningsværktøjet en reduktion på 10% i kulstofaftrykket.
”Det er nu bydende at stille spørgsmålstegn ved de fotovoltaiske forsyningskæder,” sagde Jouini. ”Ved hjælp af Rhône-Alpes-regionen inden for rammerne af den internationale udviklingsplan gik vi derfor på udkig efter spillere uden for solsektoren for at finde ny termoplast og nye fibre. Vi tænkte også på den aktuelle lamineringsproces, som er meget energikrævende. ”
Mellem trykket, pressering og afkølingsfasen, varer lamineringen normalt mellem 30 og 35 minutter med en driftstemperatur på omkring 150 C til 160 C.
”Men for moduler, der i stigende grad inkorporerer øko-designede materialer, er det nødvendigt at omdanne termoplast ved omkring 200 ° C til 250 ° C, vel vidende, at HTJ-teknologi er følsom over for varme og må ikke overstige 200 ° C,” sagde Derrier.
Forskningsinstituttet samarbejder med Frankrig-baserede induktionstermokompressionspecialist Roctool for at reducere cyklustider og skabe former i henhold til kundernes behov. Sammen har de udviklet et modul med et bageste ansigt lavet af polypropylen-type termoplastisk komposit, hvortil genanvendte carbonfibre er blevet integreret. Forsiden er lavet af termoplast og glasfiber.
"Roctools induktions -termokompressionsproces gør det muligt at varme de to forreste og bageste plader hurtigt uden at skulle nå 200 ° C i kernen af HTJ -cellerne," sagde Derrier.
Virksomheden hævder, at investeringen er lavere, og processen kan opnå en cyklustid på kun få minutter, mens den bruger mindre energi. Teknologien er rettet mod sammensatte producenter for at give dem muligheden for at producere dele af forskellige former og størrelser, mens de integrerer lettere og mere holdbare materialer.
Posttid: Jun-24-2022